The MIG solder seam is one of the most important processes in car body manufacturing.
Our MIG solder seam inspection enables the quality of soldered joints to be ensured, allowing car manufacturers to carry out precise measurements and detect defects in real time. With a combination of 2D colour evaluation and 3D height profile measurement (triangulation method) in our vision systems, car manufacturers can produce more efficiently and reduce production costs. This advanced technology makes it possible to improve soldering quality and reduce rejects.
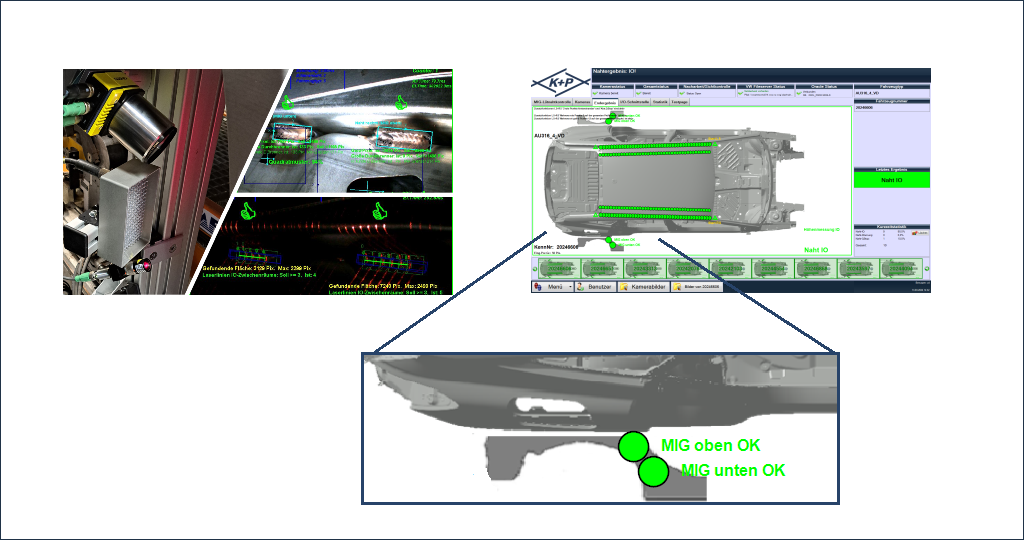
MIG Seam Visualisation of Results
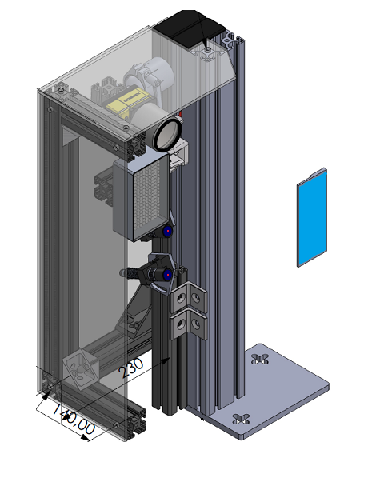
MIG100-3D System Unit
The MIG solder seam inspection system is usually installed as an additional inspection to the roof seam and includes two stationary colour cameras with powerful LED lighting KPL301 and MultiLine Laser modules for 3D measurement. The system units (camera and lighting technology) are protected in a housing and installed in the roof seam station.
There are various criteria for inspecting MIG soldered seams in order to assess the quality of this seam joining. Our MIG inspection system was developed with the aim of carrying out this inspection quickly, reliably and cost-effectively using various parameters that can be freely selected by the user.
Highlights MIG-Lötnaht
- Using Cognex In-Sight cameras – rugged hardware, standardised and very easy-to-use software KUPvision
- 2D/3D Technology – Reliable identification, measurement and detection of defects
- Extraneous light – absolutely independent of extraneous light influences
- Interfaces – FISeQS, ProfiNet, Interbus, Oracle, FuQS, XML u.w.
- Complete solutions – projects from one hand from the beginning to the system handover (Turn Key)
- Service – fast reaction times with good on-site support
How it works?
The inspection system receives the vehicle type to be inspected and the part number via the process bus (e.g. ProfiNet or Interbus) and acknowledges the data to the overoperating control (PLC). If the data is identical and all system components are ready, the start signal is given. The MIG soldering seam cameras each shoot and analyse two images (2D and 3D). At the same time, the roof laser soldered seam is scanned with the robots and sensor heads. At the end, after the robot finished signal(s), the inspection system transmits one of the three possible seam end results for roof and MIG solder seams: Seam OK, Seam Warning or Seam Qstop to the PLC.
An overview image with the final result is then generated and displayed on the PC monitor or on the second large screen in the visual inspection area. In this way, all defects and the saved images are clearly displayed to the worker. This avoids time-consuming manual searches for defects. In addition, all recorded camera images can be archived on a file server specific to the vehicle number.
Immediately after the inspection, especially for the MIG soldered seam, the results are sent to the FISeQS system (via PMON telegram) and assigned to the production process.
Example of the structure of the roof seam system with MIG soldered seam:
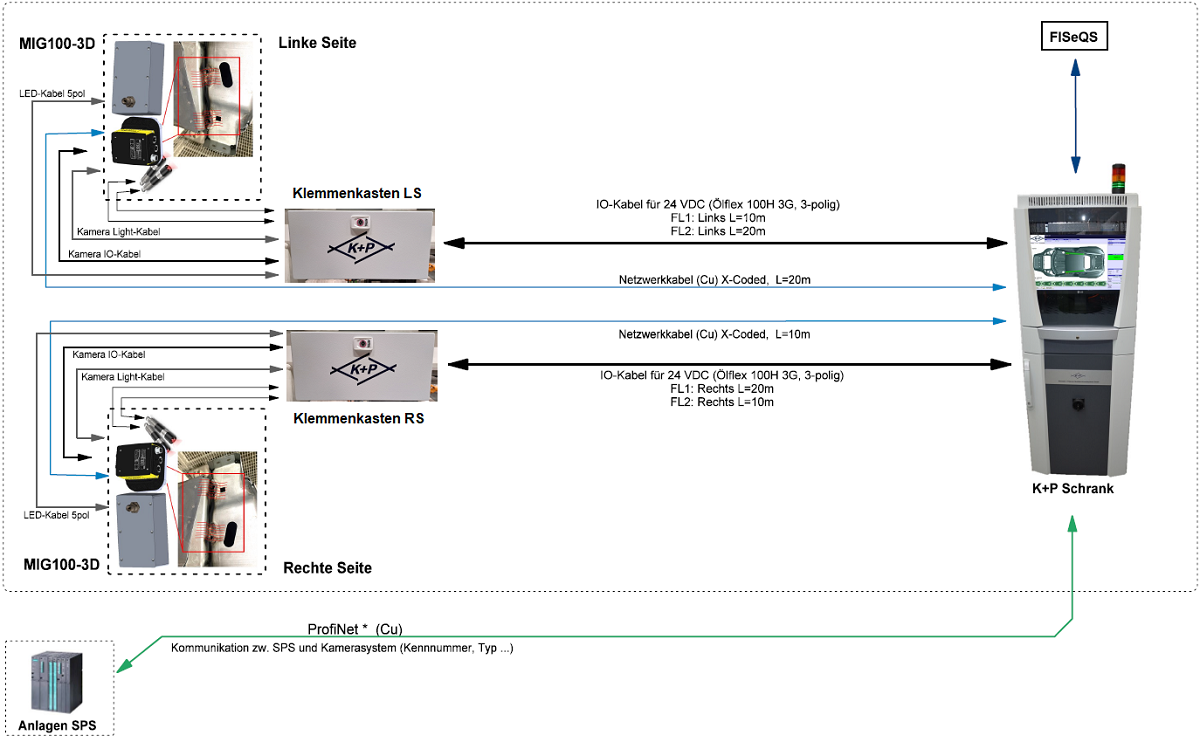
System design for MIG inspection as an extension of the roof seam system
The HMI inspection software KUPvision as standard user interface at all plants:
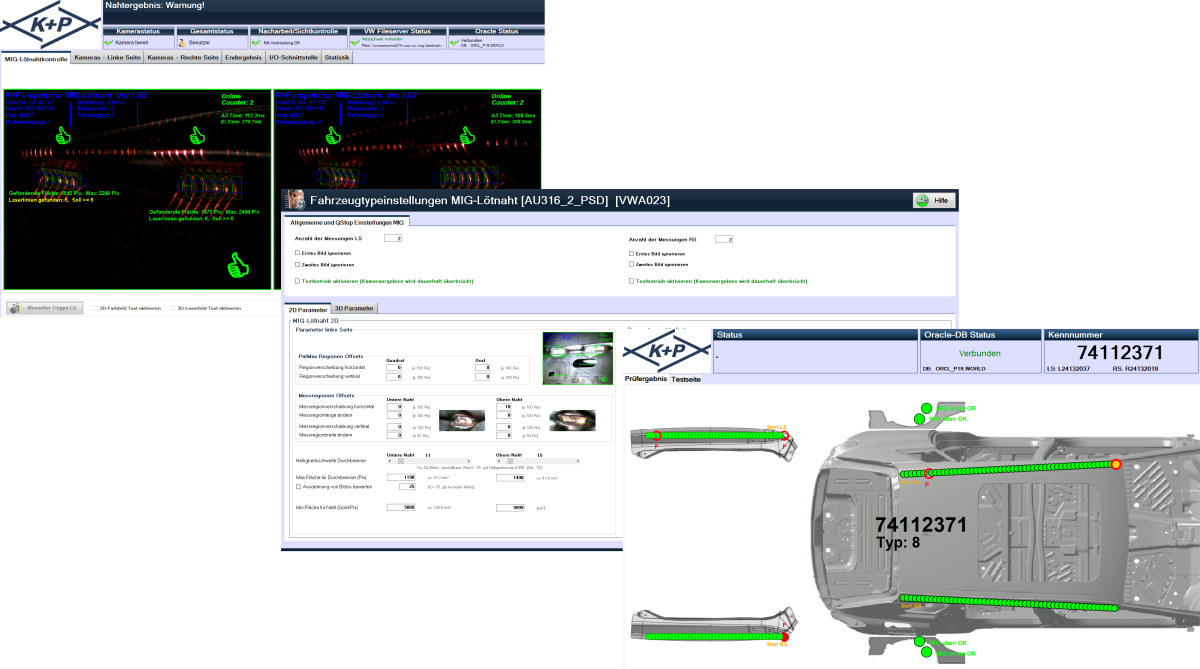
KUPvision for Seam Inspection
The following images show some examples of MIG soldered seam inspection:
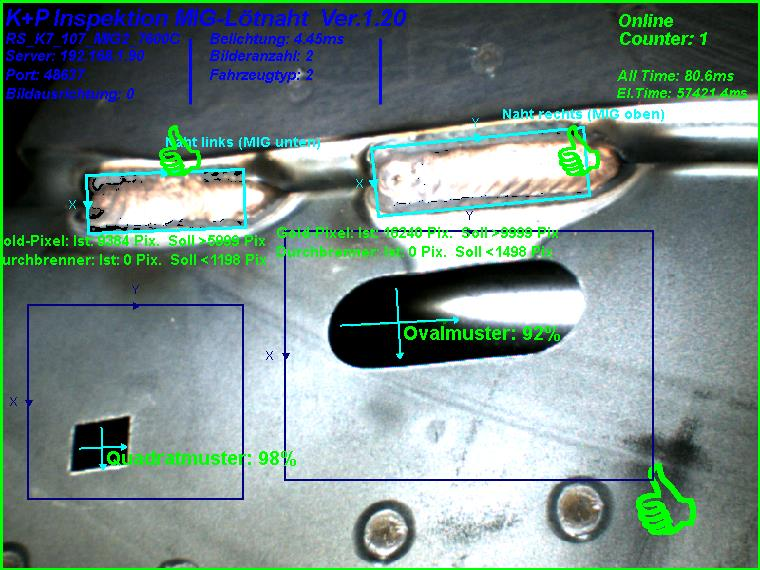
MIG 2D image with Result OK
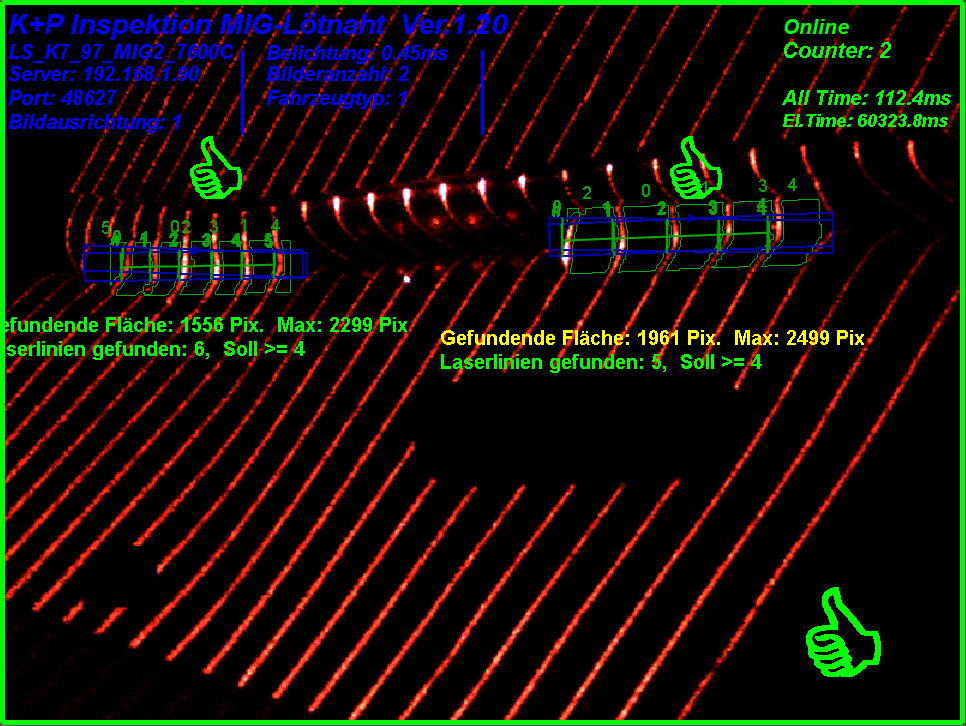
MIG 3D image with Result OK
MIG-Lötnaht NIO-Beispielbilder mit Nahteinfall bzw. Durchbrenner:
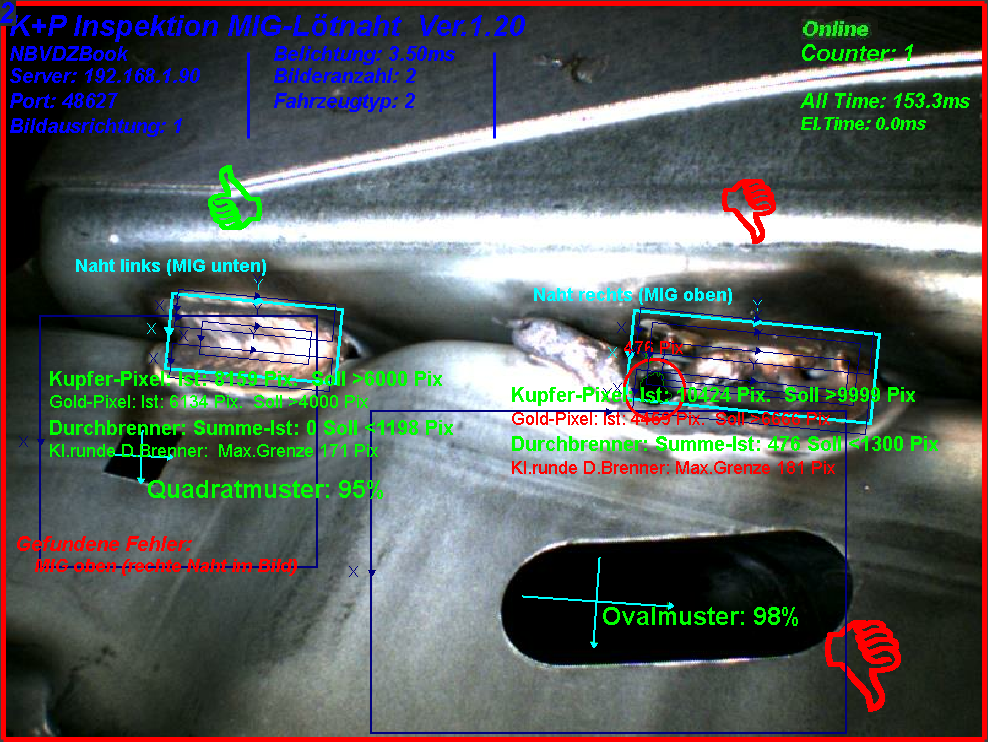
MIG 2D image with Result NOK

MIG 3D image with Result NOK